Kurt Erxleben GmbH & Co. KG
Erxleben setzt auf VISI und simuliert mit Stampack Xpress – Sicherheit statt Bauchgefühl
Der Werkzeugbau des Automotive-Zulieferers Erxleben Verformungstechnik hat CAD teilweise und CAM vollständig auf VISI umgestellt. Seither agiert man in Wildeshausen deutlich schneller und flexibler, auch was die Zusammenarbeit mit den externen Werkzeuglieferanten betrifft. Seit kurzem werden die Umformprozesse direkt aus dem VISI-Workflow heraus mit Stampack Xpress simuliert und Fehler sofort entdeckt. Ausprobieren auf der Presse und Umfräsen von Ziehstufen sind seither Vergangenheit.
Unsere bisherige Erfahrung ist: Wenn Stampack gesagt hat, es funktioniert, dann hat es auch auf der Presse hundertprozentig geklappt.
„Wir beliefern sowohl die OEMs direkt als auch die großen Zulieferer mit Blechformteilen, Schweißzusammenbauten und Zerspanungsteilen“, fasst Roman Kraus aus der Konstruktionsabteilung von Erxleben Verformungstechnik die Aktivitäten des Umformspezialisten im Automotive-Umfeld zusammen. „Ein großer Kunde von uns ist beispielsweise das nur rund 50 Kilometer entfernte Mercedes-Benz Werk in Bremen.“ Zwar werden am Standort im niedersächsischen Wildeshausen auch Neukonstruktionen erstellt, allerdings nur für kleinere Werkzeuge, die man selbst fertigt sowie für die eigenen Vorrichtungen. Denn Schwerpunkt des Werkzeugbaus sind bei Erxleben Reparatur und Instandhaltung. „Aber auch Änderungen, zum Beispiel wenn ein Teil drei Jahre lang lief und dann plötzlich Risse auftreten – das zählt zu unseren Spezialitäten.“ Alle großen Werkzeuge, vor allem die großen Folgeverbundwerkzeuge, werden deshalb extern bezogen, dort auch konstruiert und im eigenen Haus dann eingefahren. Bei diesen Werkzeugen ist die Konstruktionsabteilung jedoch stark in den Prozess eingebunden. „Das betrifft sowohl die Bewertung der Herstellbarkeit des Artikels während der Kalkulationsphase als auch die Überprüfung von Methode und Wirkflächen oder die Tryout-Phase.“ Dem Konstruktionsteam kommt dabei sowohl eine überwachende als auch eine beratende Funktion zu: „Denn wir verantworten den gesamten Optimierungsprozess, damit das Werkzeug anschließend die geforderte Qualität störungsfrei produziert. Und zwar über die gesamte Laufdauer hinweg.“
NC-Programme kamen vom Konstrukteur
Eine zusätzliche Herausforderung in der Automotivebranche ist die Forderung nach immer kürzeren Durchlaufzeiten. „Wir haben für die Optimierung meistens nur noch ein bis zwei Wochen Zeit“, verweist der Konstrukteur auf den damit verbundenen Zeitdruck. „Ohne VISI wäre das kaum umzusetzen.“ Was Roman Kraus anspricht, ist die aktuell insgesamt 22 Module umfassende Produktfamilie für den Werkzeug- und Formenbau aus dem Hause Hexagon (früher Vero Software), mit der Erxleben seinen CAD- und CAM-Workflow abbildet. „Wir starteten mit VISI 2015 bei der Fräsprogrammierung“, blickt Carsten Zejunc, der bei Erxleben den CAM-Bereich verantwortet, zurück. „Denn wir wollten hier möglichst schnell Hypermill als Programmiersystem ablösen. Damals wurde ausschließlich mit Catia V5 sowie NX konstruiert – die neben VISI heute noch als CAD-Systeme im Einsatz sind – und der Konstrukteur hatte gleich auch die NC-Programmierung mitübernommen. „Dementsprechend unflexibel waren wir beim Generieren der Fräsprogramme und suchten daher dringend nach einer Lösung, die CAD und CAM räumlich entkoppelt, die aber trotzdem durchgängig mit demselben Datenmodell arbeitet“, erinnert sich Carsten Zejunc. Zudem sollte das neue System so leicht und intuitiv zu bedienen sein, „dass ein Werkzeugmacher auch ohne große CAD-Kenntnisse schnell und fehlerfrei zu überzeugenden Fräsergebnissen kommt.“ Einschließlich simultaner 5-Achs-Bearbeitung, wie er hinzufügt. „Wir sind dann recht schnell bei VISI gelandet, nicht zuletzt auch wegen des modularen Branchenkonzepts und den wirklich durchdachten CAD- und CAM-Funktionen, die sich speziell an den Belangen des Werkzeugbaus orientieren.“ Konstruktionskollege Roman Kraus ergänzt einen weiteren Grund – VISI wird bei sehr vielen Werkzeugbauern verwendet. Nicht nur hierzulande, sondern auch in Italien und der Türkei, woher man ebenfalls Werkzeuge bezieht. Dies erleichtert die Zusammenarbeit deutlich. „Mit VISI bilden wir heute alle wichtigen Stationen unserer CAD- und CAM-Prozesse ab, von der Angebotsphase, Methodenplanung und Konstruktion bis hin zu den NC-Programmen für die Fräs- und Drahterodiermaschinen“, unterstreicht Carsten Zejunc. „Die 2,5D-Fräs-und Bohrprogramme erzeugen wir mit dem Modul VISI Compass per Featureerkennung sogar weitgehend automatisch. Das geht blitzschnell und spart uns viel Zeit.“
Umformsimulation leicht gemacht
Noch relativ neu ist das Thema Umformsimulation, berichtet Roman Kraus: „Obwohl wir dies erst seit einem halben Jahr machen, sind wir von den Möglichkeiten, die uns die Simulation bei der Blechumformung bietet, total begeistert.“ Gemeint ist die Flächen- und Volumensimulation von ein- oder mehrstufigen Metallumformprozessen mit dem Tool Stampack Xpress, das von der Stampack GmbH aus dem badischen Bietigheim entwickelt wurde. Stampack Xpress zählt als eigenständiges Tool zwar nicht zur Produktfamilie von VISI, verfolgt aber über die gleiche selbsterklärende Bedienphilosophie und lässt sich über einen, direkt in VISI aufrufbaren Dialog und der dahinterstehenden Schnittstelle in den Workflow integrieren. „So kann ich über die Analysefunktion von Stampack sofort sehen, ob und wo es nach dem Umformprozess am Teil zu Schwierigkeiten gekommen ist“, erklärt Roman Kraus. „Stampack sagt mir, wie verhält sich das Blech, liegt die Blechdicke überall innerhalb der Toleranz, welche Kräfte wirken ein, reißt etwas und so weiter.“ Stampack Xpress erlaubt dabei eine reine Schalensimulation, die vor allem bei dünnen Blechen den Vorteil hat, dass die Berechnungszeiten kurz sind. Da sich Volumen ebenfalls simulieren lassen, eignet sich das Tool auch sehr gut zur hochgenauen Simulation dicker Bleche. Durch das 3D-Simulationsmodell werden bei der inkrementellen Berechnung hier auch Spannungen und Dehnungen in Dickenrichtung berücksichtigt. Mit beiden Simulationsarten lässt sich auch die Rückfederung des Bauteils simulieren.
VISI spielt heute eine zentrale Rolle
Wie ist der VISI-Workflow im Konstruktionsbereich bei Erxleben organisiert und wo kommt Stampack Xpress zum Einsatz? Nach Umwandlung des angelieferten CAD-Modells in eine STEP-Datei – Teile werden von den Kunden häufig als native Catia- oder NX-Dateien geschickt – wird diese in VISI importiert und mit dem Modul Blank die Bauteilgeometrie sozusagen plattgedrückt und so der Platinenzuschnitt ermittelt. „Wenn sich zum Beispiel mehrere Kanten überschneiden, weiß ich, das Teil ist so nicht herstellbar und korrigiere es entsprechend“, erläutert Roman Kraus die Vorgehensweise. Aus dem Platinenzuschnitt folgt dann das Streifenlayout, aus dem sich die Anordnung und Anzahl der Umformstufen sowie die benötigte Presskraft ergeben, was wichtig für die Kalkulation der Produktionskosten ist. Ist das Teil in Ordnung, entwickelt der Konstrukteur im Vorfeld schon einmal eine vereinfachte Methode, was – in diesem Fall mit dem VISI Modul Progress – ebenfalls mit wenigen Mausklicks erledigt ist, wie Roman Kraus hervorhebt. Auf Basis dieser Erkenntnisse wird das Werkzeug von Kollegen kalkuliert, die Produktionskosten ermittelt und das Angebot verschickt. Gibt der Kunde sein Okay, unterbreiten die externen Werkzeugmacher dann auf der Grundlage dieser Informationen ihre Angebote. „In dieser Phase bekommen wir von dort zum Beispiel den Zuschnitt oder den Streifenvorschub zugeschickt, der bei uns wiederum mit VISI geprüft wird“, beschreibt Roman Kraus den Ablauf. „Da kann es zum Beispiel vorkommen, dass das Teil falsch abgewickelt wurde, dann ist auf einmal das Teil zu klein.“
Alle Problemzonen werden sofort sichtbar
Ist der Auftrag an den Werkzeugbauer vergeben, schickt dieser zeitnah die Methode. „Die schauen wir uns dann ganz genau an und überprüfen mit VISI Progress sowie seit kurzem mit Hilfe von Stampack Xpress, ob sich mit dieser Methode das Teil auch wirklich herstellen lässt.“ Das läuft wie folgt ab: „Nachdem ich mit VISI die Wirkflächenmodelle der einzelnen Ziehstufen erstellt habe, was mit Progress sehr schnell geht, exportiere ich das jeweilige Modell über die Schnittstelle in Stampack.“ Dieser Vorgang erfordert nur wenige Mausklicks. Weil Stampack Xpress extrem einfach zu bedienen ist, was Roman Kraus als Riesenvorteil ansieht, „erhält man nach wenigen Schritten und etwas Rechenzeit das Ergebnis.“ Im Analysefenster werden dann alle Problemzonen sofort sichtbar. Kraus weist in diesem Zusammenhang auf eine Funktion hin, die im Alltag von großem Vorteil ist: „Das Ergebnis lässt sich als STL-Datei exportieren. Die kann ich zum Beispiel wieder in VISI einlesen und hier gegenwirken.“ Bei den Folgeverbundwerkzeugen werden alle Umformstufen durchgerechnet, was mit Stampack über die Schrittfolge ebenfalls sehr einfach geht. Oft hängt es von Nuancen ab, ob ein Umformprozess wie vorgesehen funktioniert oder nicht, die der Konstrukteur ohne Simulation nur schwer voraussehen kann. „Früher haben wir hier vieles über den Bauch entschieden, heute lasse ich dies schön von Stampack durchrechnen.“
Schneller, flexibler und sicherer
Mit VISI hat man in Wildeshausen in Sachen Durchlaufzeit und Flexibilität einen Riesenschritt gemacht, der sich durch Stampack Xpress und der damit verbundenen Sicherheit bei der Methodenprüfung nochmals vergrößert hat, ist Roman Kraus überzeugt. Dies sieht Carsten Zejunc aus der CAM-Abteilung ebenso: „Mit VISI sind wir heute in der Lage, extrem schnell zu reagieren. Sofern der Datensatz verfügbar ist, können wir außerdem unsere Reparaturen in kürzester Zeit abwickeln.“ Denn gerade auch im Reparaturbereich bietet VISI nicht zuletzt aufgrund seines selbsterklärenden Bedienkonzepts über alle Module hinweg signifikante Vorteile. Konstrukteur Roman Kraus kommt abschließend nochmal auf die Umformsimulation zurück: „Wir haben mit Stampack Xpress heute die Möglichkeit, viele Sachen auszuprobieren, ohne damit auf die Presse gehen zu müssen.“ So entfällt auch das Umfräsen und Anpassen der Umformstufen. „Unsere bisherige Erfahrung ist: Wenn Stampack gesagt hat, es funktioniert, dann hat es auch auf der Presse hundertprozentig geklappt.“
Erxleben Verformungstechnik
Die in Wildeshausen südlich von Delmenhorst ansässige Kurt Erxleben GmbH & Co. KG produziert mit aktuell 380 Mitarbeitern Blechformteile, Schweißzusammenbauten sowie Zerspanungsteile. Neben Stanz- und Umformtechnik, bei der ein großer Maschinenpark an Exzenter- und Hydraulikpressen mit bis zu 12.000 kN Schließkraft zum Einsatz kommt, werden auch Technologien wie CNC-Abkanten, Roboterschweißen (MAG, MIG, WIG, Widerstand), 2D- und 3D-Laserschneiden, Roboterkleben oder CNC-Fräsen (3-achsig, 5-achsig) abgedeckt. Gearbeitet wird dreischichtig, die typischen Losgrößen bewegen sich zwischen 1.000 und 15.000. Aktuell gibt es rund 700 aktive Werkzeuge, mit denen chargenbezogen produziert und die im hauseigenen Werkzeugbau gewartet sowie repariert werden. Die Kunden kommen zu 99 Prozent aus der Automotivebranche. Direkt beliefert werden OEMs wie Daimler, Porsche oder Volkswagen, aber auch große Tier1 Zulieferer wie Magna CTS, Valeo, Voestalpine, Wagon Automotive oder ZF. Hierzu tragen ein ausgeprägtes Qualitätswesen sowie diverse branchenorientierte Zertifizierungen ebenso bei wie ein gut ausgebauter Logistikbereich.
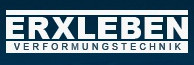
Kurt Erxleben GmbH & Co. KG
Wilhelm-Maybach-Str. 1
27793 Wildeshausen
Telefon: + 49 (0) 4431 – 70 960
Email: vertrieb@erxleben.biz
Web: www.erxleben.biz