FASSNACHT Werkzeug- und Formenbau
Weiterer Schritt in Richtung Zukunft – FASSNACHT Werkzeug- und Formenbau verzahnt VISI noch enger mit der Automatisierung.
Spritzgießwerkzeuge ‚Made by FASSNACHT‘ genießen einen Spitzenruf. Seit vielen Jahren schon trägt im CAD/CAM-Bereich die modulare 3D-Branchenlösung VISI entscheidend zum Erfolg der in Bobingen nahe Augsburg ansässigen Werkzeugmanufaktur bei. Auch die Fräs- und Senkerodierzelle ‚Chameleon‘ ist hier nun komplett in den VISI-Workflow eingebunden, in der seit Kurzem sogar die Elektroden- und Bauteilkontur automatisch kontrolliert wird.
Wir sind nicht nur deutlich schneller, sondern auch genauer geworden. …
Zweifellos kann man den FASSNACHT Werkzeug- und Formenbau als hochinnovative Werkzeugmanufaktur bezeichnen, die Wissen und Hightech auf geradezu ideale Weise kombiniert. Hightech bedeutet, dass in Bobingen nicht nur mit hochmodernem Maschinenequipment bis in den μ-Bereich gefertigt wird, sondern auch das Thema Automatisierung inzwischen einen hohen Stellenwert einnimmt. Und das ist nicht zu übersehen. Denn beim Gang durch die helle Fertigungshalle fällt der Blick schnell auf einen Linearroboter, der hinter Glaswänden auf den siebeneinhalb Meter langen Schienen der Fertigungszelle hin und her surrt. Etwa 5.000 Elektroden aus Grafit werden wohl pro Jahr in dieser Anlage (Chameleon von Zimmer+Kreim) rund um die Uhr automatisch gefräst, vermessen, zwischengelagert und in die zwei Erodiermaschinen (Z+K Genius 1000) eingewechselt, schätzt Firmenchef Wolfgang Faßnacht. Denn die Anlage ist in dieser Ausbaustufe noch kein ganzes Jahr in Betrieb. 2017 wurde sie nacheinander zunächst mit einer CNC-Messmaschine (Zeiss Duramax) und ein paar Monate später mit einer 5-achsigen Röders RXP601-DSH erweitert. „Das Anlagenkonzept ermöglicht es, dass sich die einzelnen Stationen auch manuell nutzen lassen – und die automatische Abarbeitung der Aufträge im Hintergrund trotzdem weiter läuft”, erklärt Faßnacht. „Deshalb verwenden wir die Messmaschine sowie die neue Röders auch für Aufgaben außerhalb der Elektrodenfertigung.“ Die HSC-Maschine übernimmt bei FASSNACHT zum Beispiel auch das hochpräzise Hartfräsen von Formeinsätzen oder -kernen auf Fertigmaß. So sind die Maschinen stets gut ausgelastet, was mehr Spielraum in der Kalkulation lässt, und die Flexibilität bleibt trotzdem gewahrt. Entscheidend sei für ihn gewesen, dass eine Automatisierungslösung nahtlos in die vorhandene CAD/CAM-Struktur eingebunden ist, betont Faßnacht. „Das haben wir hundertprozentig umgesetzt.”
Schon seit 17 Jahren im Einsatz
In Bobingen arbeitet man in diesem Bereich ausschließlich mit der 3D-Branchenlösung VISI des britischen Herstellers VERO Software. Mit weltweit über 30.000 Installationen und den zahlreichen, eng verzahnten Modulen für Konstruktion, Simulation, Produktdatenverwaltung (PDM) und Fertigung ist VISI speziell auf die Anforderungen des Werkzeug- und Formenbaus ausgerichtet. Die aktuell 18 VISI-Module lassen sich je nach Bedarf zusammenstellen und jederzeit durch weitere Elemente ausbauen. Das System bietet Schnittstellen zu allen wichtigen Datenformaten, die ebenfalls als einzelne Module erhältlich sind. FASSNACHT bildet mit VISI seinen gesamten Workflow ab, angefangen von der Angebotsphase über die Konstruktion bis hin zu den NC-Programmen für die Fräs- und Erodiermaschinen. Mit VISI hatte man bereits um den Jahrtausendwechsel herum begonnen. Bei FASSNACHT war man dann von Anfang an von den 3D-Modellierfunktionen und dem in sich stimmigen Branchenkonzept von VISI begeistert. Die Entscheidung, damals zu VISI zu wechseln, hätte nicht zuletzt auch MECADAT leicht gemacht, der VISI-Distributor für den deutschsprachigen Raum, dessen Service, Know-how und Preisgestaltung überzeugt hatte.
VISI-Bedienkonzept unterstützt die Flexibilität
Heute ist VISI in Bobingen mit diversen Modulen an insgesamt 12 Arbeitsplätzen installiert. Hinzu kommen drei Lizenzen für den VISI Viewer. Somit arbeiten statistisch rund die Hälfte der Belegschaft mit einem oder mehreren Modulen von VISI. Ein fünfköpfiges Team ist dabei mit den speziell für den Kunststoffbereich ausgelegten VISI-Modulen wie Mould, Split und Analyse oder der Bauteilbibliothek ausschließlich für die Werkzeugkonstruktionen zuständig. Firmenphilosophie ist seit vielen Jahren schon, dass nur die formgebenden Bereiche wie Kavitäten, Kerne oder Auswerfer selbst gefertigt werden. Alles andere bezieht man von großen Zulieferern wie Meusburger oder Knarr, was auch den gesamten Formaufbau einschließlich der fertig bearbeiteten Platten einschließt.
Nicht zuletzt das über alle Module durchgängige und genial einfache Bedienkonzept von VISI dürfte in Bobingen dazu beitragen, dass die NC-Programmierer, die grundsätzlich alle auch an den Maschinen arbeiten, zum Großteil die Elektroden selber konstruieren. „Denn wer mit den Fräs- und Senkerodiermaschinen arbeitet, kennt sich mit Elektroden einfach besser aus”, ist Faßnacht überzeugt. Zum Beispiel beim Umgang mit Parametern wie Erodierspalt oder der Aufteilung der Elektroden, was der Werkzeugkonstrukteur oft nur schwierig beurteilen kann. Natürlich springt Letzterer bei Engpässen auch schon mal bei der Elektrodenableitung mit ein. Schließlich sitzen die Konstrukteure und Programmierer im selben Büro an den Schreibtischen gegenüber, getrennt nur durch eine Tür von der Werkstatt.
Den CAM-Bereich verantworten in Bobingen acht Mitarbeiter. VISI beliefert dabei die drei 5-achsigen Fräszentren von DMG Mori sowie die beiden Drahterodiermaschinen (Mitsubishi MV2400R und FA20) mit den benötigten NC-Daten. Und wie von Faßnacht bereits angesprochen, ist die Chameleon-Fertigungszelle besonders eng mit VISI verzahnt, wobei hier dem Modul VISI Elektrode eine besondere Bedeutung zukommt. VISI versorgt dabei die hier integrierte 5-achsige Röders mit Fräsprogrammen, zudem beziehen die beiden Senkerodiermaschinen Genius 1000 über VISI-Elektrode alle relevanten Informationen für den Erodierprozess – und die Messsoftware Calypso des Zeiss-Koordinatenmessgeräts beschickt VISI mit Versatzdaten sowie den Daten zur Qualitätssicherung. Im Mittelpunkt steht dabei die von Z+K entwickelte modulare Zellensoftware, Alphamoduli genannt, die alles koordiniert.
Elektrodenkonstruktion weiterhin lieber manuell
Am Anfang des CAM-Workflows für den Senkerodierbereich steht die Elektrodenkonstruktion. Natürlich lag auch bei FASSNACHT der Wunsch nahe, dass nicht nur das Elektrodenfräsen und das Erodieren komplett automatisch ablaufen, sondern ebenso die Elektrodenkonstruktion. „Dies ist mit VISI-Elektrode auch weitgehend möglich, sofern es sich um Standardelektroden mit einfachen Konturen handelt”, berichtet Thomas Brugner, der bei FASSNACHT zum vierköpfigen Team gehört, das das Chameleon betreut. „Wenn jedoch Verrundungen und komplexere Geometrien ins Spiel kämen, konstruiere ich die Elektroden lieber von Hand.” Dies würde mit VISI Elektrode mittlerweile aber dermaßen einfach und schnell gehen, dass der Mehraufwand kaum ins Gewicht fallen würde. Und Brugner nennt einen weiteren Grund, der für die manuelle Vorgehensweise spricht: „Da wir heute fast ausschließlich mit Grafit erodieren, lassen sich die Elektroden gut zusammenfassen, weil wir viel dünner und tiefer fräsen können.” Gut sei zudem, dass VISI Elektrode über die Elektrodenkonstruktion hinaus auch die Verwaltung der nachgelagerten Prozesse deutlich vereinfachen würde. „Zusammen mit dem Grundmaß der Elektrode wähle ich bei VISI immer auch gleich den Halter aus. Da der Nullpunkt bei uns über den Halter definiert ist und die Abmessungen vom Grundkörper vorgegeben sind, spanne ich am Rüstplatz nur noch das Rohteil auf und hänge das Ganze in den Schrank.” So ist der Nullpunkt auch im Chameleon definiert, und zwar über alle Stationen hinweg.
Grafitfräsen jetzt überwiegend 5-achsig
Ist dann die Elektrode fertig konstruiert, das benötigte Material – sofern nicht auf Lager – bestellt, werden mit VISI Machining die NC-Sätze programmiert, die Rohlinge vorbereitet sowie Zubehör wie Halter oder Spannsysteme bereitgestellt. „Seit wir das Chameleon mit der Röders RXP601-DSH erweitert haben, fräsen wir die Elektroden überwiegend 5-achsig”, erklärt Brugner. Für ihn hätte das 5-Achs-Elektrodenfräsen auf einer sehr stabilen und genauen Maschine wie der Röders klare Vorteile, was sich gegenüber dem bisherigen 3-achsigen Fräsen auf der Vorgängermaschine äußerst positiv bemerkbar machen würde. So könne man zum Beispiel mit kürzeren und damit stabileren Werkzeugen wesentlich kompliziertere Konturen fräsen und so die Anzahl der benötigten Elektroden reduzieren. „Wo ich früher schon mal zwanzig Elektroden benötigt habe, reichen heute oft zehn.” Simultan fräse man die Elektroden allerdings so gut wie nicht. „Der Anteil beläuft sich hier auf unter drei Prozent.”
Grundsätzlich wird beim anschließenden Datentransfer an das Chameleon-System jedes Bauteil dem jeweiligen Fräsprogramm zugeordnet. Dabei hilft ein Automatismus. Aus VISI findet also immer nur ein einziger Importvorgang statt – inklusive Fräsprogramm, der Information der Zellensoftware über die Anzahl der Elektroden sowie dem Messprogramm, das über die Calypso-Messsoftware automatisch die Versatzdaten kontrolliert.
Elektrodenkontur wird ebenfalls automatisch gemessen
In der Praxis läuft das in Chameleon vom Prinzip her genauso ab wie beim Messen der Versatzdaten: Nach dem Fräsen geht es per Roboter auf die Messmaschine, wo die Versatzdaten überprüft werden. Die Kontur wird dann anhand der von VCheck vorgegebenen Punkte und der mitgelieferten Anfahrwege automatisch gemessen. Sind alle Maße in der Toleranz, gibt die Zellensoftware die Elektrode zum Erodieren frei. „Die Kontur messen wir allerdings nur bei den wichtigen Trennungselektroden, wo wir ein sehr exaktes Maß benötigen”, schränkt Thomas Brugner ein. Bei Elektroden, beispielsweise für einen Steg oder eine Versteifungsrippe, sei diese Kontrolle hingegen unnötig. Begeistert ist er in diesem Zusammenhang über die Flexibilität, die das Anlagenkonzept in diesem Bereich bieten würde: „Nehmen wir an, ich benötige für einen Auftrag acht Schlichtelektroden, und bei einer stimmen die Konturmaße nicht, weiß dies die Z+K-Software und erodiert vorab mit den sieben Elektroden.”
Die Frage, ob die erweiterte Automatisierungslösung für seinen Bereich nun echte Vorteile bieten würde, beantwortet Brugner mit einem klaren Ja. „Wir sind nicht nur deutlich schneller, sondern auch genauer geworden.” Auch Firmenchef Faßnacht ist mit dem Erreichten sehr zufrieden. Natürlich benötige Automatisierung immer eine gewisse Anlaufzeit und mache eine genauere Planung der Prozessschritte erforderlich. „Alleine schon die hohe Maschinenauslastung ist für uns ein klares Plus.” Genauso wichtig aber sei, dass man hinsichtlich Durchlaufzeit und Qualität ebenfalls ein gutes Stück vorangekommen ist. „Ohne VISI und den guten Support von MECADAT wäre dies alles wohl nur schwer zu erreichen gewesen”, ist Faßnacht überzeugt.
FASSNACHT Werkzeug- und Formenbau
Spritzgießwerkzeuge ‚Made by FASSNACHT‘ stehen heute im Ruf, zu den besten zu zählen, die der Markt zu bieten hat. Hiervon zeugt nicht zuletzt auch die mehrmalige Auszeichnung als ‚Werkzeugbau des Jahres‘. 1990 vom Werkzeugmachermeister Wolfgang Faßnacht in Augsburg gegründet, entwickelte sich aus einer 3-Mann-Firma in kurzer Zeit ein Hightech-Unternehmen für Spritzgießformenbau mit höchsten Qualitätsanforderungen, das heute 23 Mitarbeiter beschäftigt und seinen Firmensitz in Bobingen hat. Das umfangreiche Dienstleistungsangebot umfasst die Beratung bei der Auslegung von Bauteilen oder die Gestaltung von Produktionslösungen ebenso wie den Bau von Prototypen. Abgedeckt wird eine ganze Bandbreite von – meist hochkomplexen – Spritzgießwerkzeugen, die für Mehrkomponenten- oder Gasinnendrucktechnik ebenso ausgelegt sein können wie für Folienhinterspritzungen oder Dünnwandtechnologien. Pro Jahr durchlaufen etwa 50 bis 60 Spritzgießwerkzeuge mit einem Gewicht von unterhalb 4,5 Tonnen die Fertigung, davon etwa 40 Prozent 2K-Werkzeuge. Konstruiert werden alle Werkzeuge im eigenen Haus.
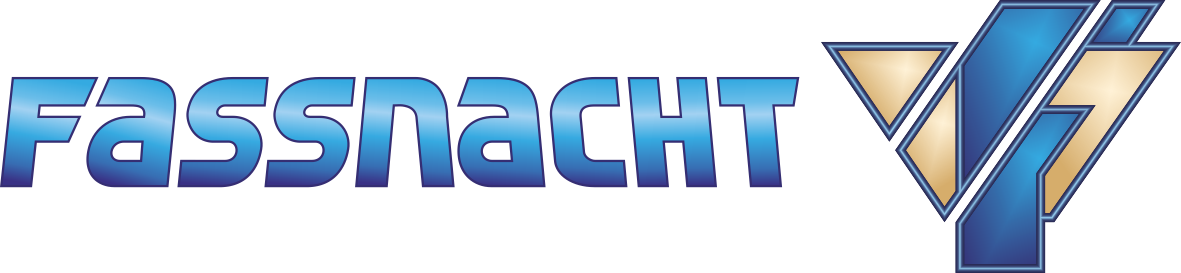
FASSNACHT Werkzeug- und Formenbau
Boschstr. 12a
86399 Bobingen
Telefon: + 49 (0) 8234 – 96 540
Email: formenbau@fassnacht.tools
Web: www.fassnacht.tools