ERBIWA GmbH
Ideenschmiede auf der Überholspur – ERBIWA GmbH wächst seit Jahren und setzt bei CAD und CAM komplett auf VISI
Seit der Gründung vor dreizehn Jahren stehen die Zeichen bei ERBIWA in Lindenberg auf Wachstum. Denn die Westallgäuer verstehen sich nicht nur als Spezialist für Hinterspritzwerkzeuge, sondern auch als Ideenschmiede für designorientierte Hightech-Oberflächen und Komponenten. Von Beginn an setzte ERBIWA bei 3D-CAD und Füllsimulation auf VISI – seit Kurzem auch beim Fräsen.
Die dynamische Simulation der Bewegungen sehe ich in VISI als echtes Highlight an
ERBIWA sieht sich als Denkfabrik mit Schwerpunkten auf Konstruktion, Projektmanagement, Montage und Musterung. „Unsere Firmenphilosophie ist, über ein Netzwerk von Spezialisten maßgeschneiderte Komplettlösungen im Kunststoffbereich überall dort anbieten zu können, wo auch unsere Kunden aktiv sind“, erläutert Matthias Wagner, der Sohn vom Firmengründer und Technische Leiter der ERBIWA GmbH. Die Kunden kommen überwiegend aus der Automotivbranche, weshalb man mit eigenen Standorten in den USA und in China vertreten ist. Die Wurzeln des Unternehmens liegen allerdings im Allgäu. „Als 2005 mein Vater Ernst und seine Frau Brigitte Wagner die Firma ERBIWA GmbH gründeten, wurde neben der Konstruktion von Spritzgießwerkzeugen von Anfang an der Schwerpunkt auf das Projektmanagement gelegt.“ Seither wurde die Strategie verfolgt, durch konsequente Einbindung von Partnern dem Kunden gegenüber als Komplettanbieter im Werkzeugbau aufzutreten und die Fertigungstiefe trotzdem gering zu halten.
So kam es bald zu den ersten Projekten mit einem nahe gelegenen Unternehmen, das auf die Entwicklung und Produktion von Aluminiumdekorteilen für die Automobilindustrie spezialisiert war. Bei diesem Unternehmen wurden Aluminiumschalen erstmals direkt hinterspritzt, was bisherige Klebe- oder Crimpprozesse unnötig machte. Der Bedarf an Spritzgießwerkzeugen stieg darum stark an und man suchte nach einem starken Partner in diesem Bereich. „Zusammen sind wir dann schnell gewachsen und so in den Fahrzeuginnen- und Dekorbereich hineingekommen, der heute den Schwerpunkt unserer Aktivitäten bildet“, blickt Matthias Wagner zurück.
Werkzeugkonstruktion von Beginn an mit VISI
Die Allgäuer Erfolgsgeschichte ist auch eng mit dem integrierten 3D-CAD- und CAM-System VISI verbunden, eine Produktfamilie für den Werkzeug- und Formenbau, die von dem britischen Hersteller VERO Software entwickelt und weiter ausgebaut wird. Die Entscheidung, auf VISI zu setzen, fiel 2005 relativ schnell: Bei der damaligen Marktrecherche wurde rasch klar, dass VISI sehr gut auf die Bedürfnisse im Werkzeug- und Formenbau zugeschnitten ist. Während am Anfang klar Werkzeugkonstruktion und Produktentwicklung gepaart mit Projektmanagement bei ERBIWA im Vordergrund standen und dies mit VISI abgebildet wurde, kam nach einer steilen Wachstumsphase 2014 der Fräsbereich hinzu.
Bei ERBIWA werden – zumindest bis vor Kurzem – alle Teile und Komponenten eines Werkzeugs zugeliefert: Formaufbauten, Heißkanalsystem und Normalien bezieht man von den einschlägigen Anbietern wie Meusburger, Hasco oder Knarr, formgebende Bereiche wie Kavitäten, Kerne oder Schieber lässt man bei Partnern aus der Umgebung fertigen – und seit 2013 auch in China. „Denn unsere Automotiv-Kunden hatten wiederholt den Wunsch geäußert, dass ERBIWA auch in Asien und vor allem in China präsent sein sollte”, berichtet Matthias Wagner den Hintergrund dieses Vorhabens. Nach einigen nicht so überzeugenden Firmenbesuchen fand Ernst Wagner schließlich einen Werkzeugbau- und Spritzgussspezialisten, der für die geplanten China-Aktivitäten exakt zu passen schien. Die zweijährige Kooperation verlief dann so erfolgreich, dass 2015 ein Joint-Venture gegründet wurde, die ERBIWA Mould Industrial Co.Ltd.
Chinesische Tochter fährt heute die Grundlast
Von der chinesischen Joint-Venture-Tochter bezieht man heute fast alle individuell gefertigten Teile, aus denen im Allgäu dann für heimische Kunden das fertige Werkzeug montiert wird. Den chinesischen Markt – das betrifft auch die dort aktiven deutschen Kunden – beliefert die ERBIWA Mould Industrial direkt mit Werkzeugen. Bei kleinen Teilen fährt man allerdings mehrgleisig, „was auch mit Werkzeugen für nachgelagerte Prozesse zur weiteren Oberflächenveredelung zu tun hat, die hier am Standort gefertigt werden.“ Dazu wurde parallel in Lindenberg eine eigene Fräsfertigung aufgebaut, wovon zwei neu angeschaffte 3-achsige Bearbeitungszentren zeugen, die mit dem CAM-Modul Machining ebenfalls in den VISI-Workflow eingebunden sind. Mit diversen Modulen ist VISI an insgesamt elf Arbeitsplätzen installiert, ergänzt durch sechs Lizenzen für den VISI Viewer. Sowohl bei CAD als auch bei CAM bildet im 3D-Bereich grundsätzlich VISI Modelling die Grundlage, das durch Module aufgabenspezifisch ergänzt wird. Bei ERBIWA ist dies im Konstruktionsbereich VISI Mould, das um die fertigen Formeinsätze herum einen weitgehend automatisierten Werkzeugaufbau ermöglicht.
Verfechter des direkten Konstruierens
Beim 3D-CAD-Grundmodul VISI Modelling handelt es sich um einen sogenannten Hybridmodellierer. Dieser Begriff meint, dass VISI den hier verwendeten Parasolid-Kern für die Volumenmodellierung sowie für die Flächenmodellierung kombiniert nutzt. Im Gegensatz zu rein parametrisch arbeitenden CAD-Systemen hat dies im Werkzeugbau klare Vorteile, da man deutlich schneller und flexibler konstruieren kann.
„Wir sind ein Verfechter des direkten Konstruierens, was mit VISI ja sehr gut funktioniert”, meint Wagner und ergänzt: „Ich habe früher mit anderen namhaften CAD-Systemen, welche parametrisch aufgebaut sind, Werkzeuge konstruiert, und bin deshalb von der Einfachheit, die VISI hier bietet, wirklich begeistert.“ So kommt es zum Beispiel im Alltag häufig vor, dass ein Mitarbeiter der insgesamt achtköpfigen Konstruktionsabteilung das Werkzeug komplett fertig konstruiert hat, und später ein Kollege und vielleicht noch ein weiterer Anpassungen oder Veränderungen vornehmen würden. Da wäre es mit parametrischen Konstruktionsdaten nicht so einfach, den Einstieg zu finden. „Denn da müssten die anderen Kollegen erst mal verstehen, mit welcher Philosophie das Werkzeug aufgebaut wurde. Jeder hat eben doch seinen eigenen Stil und geht etwas anders vor.“ Selbst einfachste Änderungen würden dann sehr viel Zeit in Anspruch nehmen, ist der Technische Leiter überzeugt. „Das geht mit VISI bei uns sehr einfach, unkompliziert und ohne Qualitätsverlust.“
Parametrik bei der Bewegungssimulation
Die VISI-Parametrik setzt man bei ERBIWA hauptsächlich bei der Simulation von Bewegungsabläufen ein. „Wir simulieren beispielsweise die Bewegungen der Schrägschieber: Bekommen wir die Teile problemlos entformt oder besteht die Gefahr in Kollision mit dem Bauteil oder mit anderen Werkzeugkomponenten zu fahren? Das können wir dann mit VISI sozusagen stufenlos über den gesamten Hub hinweg darstellen.” Auch Drehbewegungen von Zahnrädern, die über Zahnstangen ausgeführt werden, sind ein typischer Fall für die Simulation. Oder das Betrachten von Schieber mit Schrägbolzen bei der Öffnung des Werkzeugs, wobei man diese Technik relativ wenig verwendet und dies lieber über Zylinder steuert. „Wo es früher Probleme gab, kommen wir heute mit der Kinematik-Simulation sehr schnell zu Ergebnissen“, unterstreicht Matthias Wagner. „Die dynamische Simulation der Bewegungen sehe ich in VISI als echtes Highlight an.“
VISI Flow sorgt für korrekte Anspritzpunkte
Mit dem Modul VISI Flow stellt man bei ERBIWA bereits seit zehn Jahren sicher, dass die zu produzierenden Teile über optimale rheologische Eigenschaften verfügen. Denn alle Phasen des Spritzgießprozesses, die im Werkzeug ablaufen, werden damit per FEM-Füllsimulation (Finite Elemente Methode) konstruktionsbegleitend analysiert. Das funktioniert im Alltag sehr gut, die Simulation wird direkt aus dem 3D-CAD von VISI heraus gestartet. „So können wir einfach Anspritzkonzepte und Füllverhalten anschauen und miteinander vergleichen und sehen ziemlich schnell, ob es beispielsweise zu Temperatur- oder Luftproblemen kommt”, erklärt Wagner. „Nach Bedarf setzen wir das Modul auch für Verzugsberechnungen ein.“
CAD-Daten von und nach China über Parasolid
Ein weiteres Merkmal ist im Konstruktionsalltag von besonderer Bedeutung, nämlich die guten Importfunktionen, die VISI in Form diverser Schnittstellen von Haus aus mitbringt, so Wagner. „Das ist für uns sehr wichtig: Zum einen die Kundendaten betreffend, und zum anderen für unsere Zusammenarbeit mit unseren chinesischen Kollegen.“ Denn alle CAD-Daten werden hier über Parasolid ausgetauscht. Hintergrund ist, dass bei ERBIWA Mould Industrial mit Siemens NX konstruiert wird. Heute finden zum Teil auch Konstruktionen in China statt, die in Lindenberg dann noch modifiziert werden. „Damit haben wir sehr gute Erfahrungen gesammelt und das läuft über die Parasolid-Schnittstelle von VISI absolut problemlos.“
Mit VISI haben die Allgäuer ein wirklich durchgängiges System im Haus, „mit dem wir anhand desselben 3D-Modells auf Basis von Parasolid konstruieren und fräsen”, zieht der Technische Leiter Bilanz. „Es gibt keinen Verlust an Datenqualität.“ Lob verdient auch das selbsterklärende Bedienkonzept, das die Einarbeitungszeit von neuen Mitarbeitern auf ein Minimum reduziert. „Dies macht eine externe Schulung oft unnötig, auch dank des großen Erfahrungsschatzes, den wir uns im Haus bei VISI erarbeitet haben.“ Aber auch den Service von MECADAT lobt Matthias Wagner. Der VISI-Distributor für den deutschsprachigen Raum überzeugt nicht nur bei der Preisgestaltung, sondern vor allem auch in Sachen Know-how. „Ohne diesen Support hätten wir mit VISI in der Konstruktion nicht so schnell den hohen Stand erreicht, den wir heute haben.“
ERBIWA GmbH
Seit Gründung 2005 in Röthenbach im Westallgäu hat sich die heute im benachbarten Lindenberg ansässige ERBIWA GmbH von einem Konstruktionsbüro für Spritzgießwerkzeuge zu einem Unternehmensverbund mit aktuell 136 Mitarbeitern entwickelt. 55 davon sind bei ERBIWA Mould Industrial beschäftigt, der 2015 zusammen mit einem Kooperationspartner gegründeten Joint-Venture-Tochter im chinesischen Dongguan. Bereits 2007 wurde in den USA die ERBIWA LLC gegründet. Aktuell fokussiert ERBIWA überwiegend den Automotivbereich. Zweistellige Zuwachsraten zeugen davon, dass man in der noch recht jungen Firmengeschichte so gut wie alles richtig gemacht hat.
Im Werkzeugbau liegt die Kernkompetenz bei Hinterspritzwerkzeugen mit bis zu sieben Tonnen Gewicht für Komponenten aus dem Fahrzeuginnenbereich, was auch die Unterstützung bei der Artikelentwicklung umfassen kann. Hinterspritzt werden die Oberflächen Edelstahl, Aluminium, Holz oder Carbon. Hinzu kommen 2K-Werkzeuge, unter anderen mit Sperrschiebertechnik (ohne Drehteller), Gas- und Wasserinnendrucktechnik (GID / WID), Stanz-Umformwerkzeuge für Aluminium-, Holz- oder Edelstahlblenden und Werkzeuge für nachgelagerte Prozesse zur weiteren Oberflächenveredelung.
ERBIWA tech GmbH
Bereits 2008 wurde mit der Serienproduktion von Kunststoffteilen begonnen, wofür die ERBIWA tech GmbH zuständig ist. Schwerpunkt sind Sicht- und Dekorteile für den Automotivbereich wie Radnabenabdeckungen oder hinterspritzte Zierblenden, die meist in mittleren Losgrößen zwischen 5.000 und 50.000 Stück gespritzt werden. Seit 2015 liefert man als Tier-1 Lieferant bei BMW sogar direkt ans Band. „Zudem nutzen wir den Spritzgießbereich auch als Technikum, um neue Werkzeuge zu bemustern, Prototypen herzustellen oder Funktionen von Handlingsystemen wie Roboter oder Greifer zu erproben”, erläutert Matthias Wagner die dahinterstehende Idee.
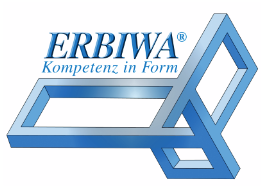
Erbiwa GmbH
Westpark 6
88161 Lindenberg
Telefon: + 49 (0) 8381 – 80 72 330
Email: info@erbiwa.com
Web: www.erbiwa.com